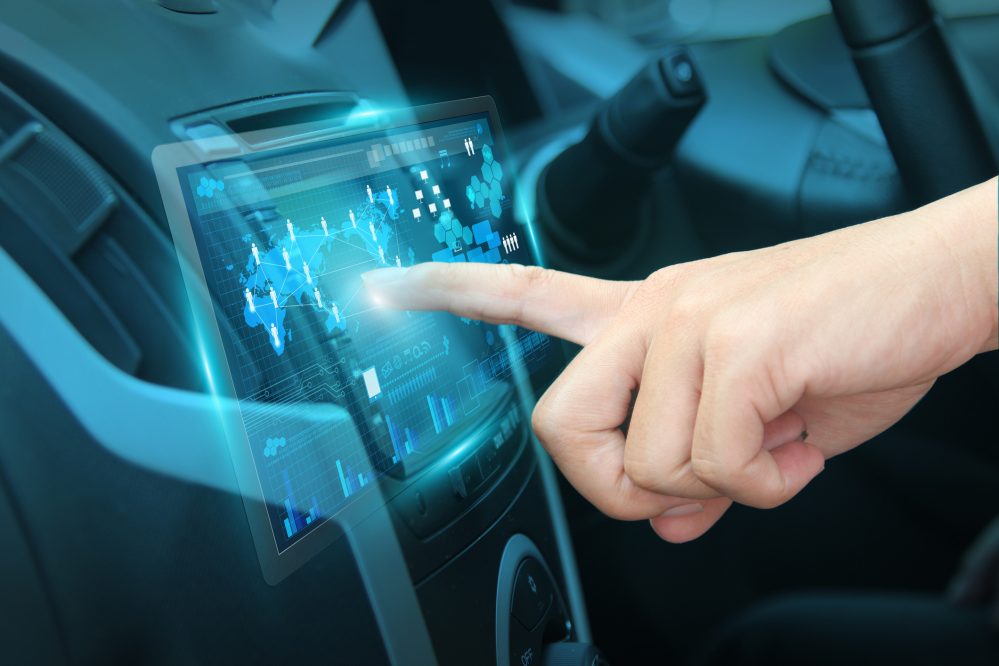
EMBRACE THE FUTURE
It’s uncomfortable, it’s frustrating, sometimes it’s even something to fear… and in the automotive industry, it’s unavoidable.
Independent auto repair shop ownership and management are no strangers to change. Technological innovations and societal trends disrupt our industry every few years, forcing us to train in new ways, buy new tools, and adopt new ideas. But we can already see the next round of changes coming to our industry, and it’s now more important than ever to be prepared, and to be ready to embrace new ways of running your business!
First and foremost, the national shortage of technicians is a major problem and one we’ll be dealing with for quite some time. Our society as a whole has devalued skilled trades, meaning that for years now, young people have been hearing at home and at school how they should be avoiding careers like automotive technician!
Kids simply aren’t aware of the opportunities that skilled trade training can offer them. As a result, the average age of a mechanic in the United States has gotten older and older – currently somewhere in the mid-40s.
While this is a large-scale problem that is beyond your shop’s immediate control, you can still take steps to ensure that the impact of a labor shortage isn’t felt as harshly as it could be – starting with taking a good hard look at the systems you use in your daily operation.
One problem a lot of shops seem to inflict upon themselves is putting up too many barriers for techs to be efficient.
Here’s a common example: the tech has to use programs that don’t talk to each other. So when he wants to use a labor guide, he has to copy the VIN from his point of sale, paste it into a labor guide, use endless dropdown menus to find the labor time…and then repeat the process when he searches for a second labor guide to compare.
And that all assumes that he didn’t get logged out by another tech doing their own labor guide lookup.
The amount of time techs have to spend logging into websites and typing the same search terms is staggering, not to mention inefficient and unproductive.
And what if that young technician overcomes these inefficiencies, comes to love their career, and eventually wants to set out and own a shop of their own? They get to look forward to the same — only now it’s not just one facet of their job that’s inefficient, it’s all of them. Their marketing program doesn’t communicate with the point of sale. Their labor guides don’t talk to the repair order estimates. Their inspections don’t work closely with the parts ordering. Each component of their job, in every phase of the repair, is managed by a different software, part of a different subscription, and each is sucking the hours out of their day, out of their employees’ days, and out of their customers’ days. Hours….AND money.
It’s really no wonder that we’re facing a national technician shortage in the automotive industry, when that’s what we have to put up with just to do a job we love!
Click HERE to continue reading this article in Motor Age Magazine.